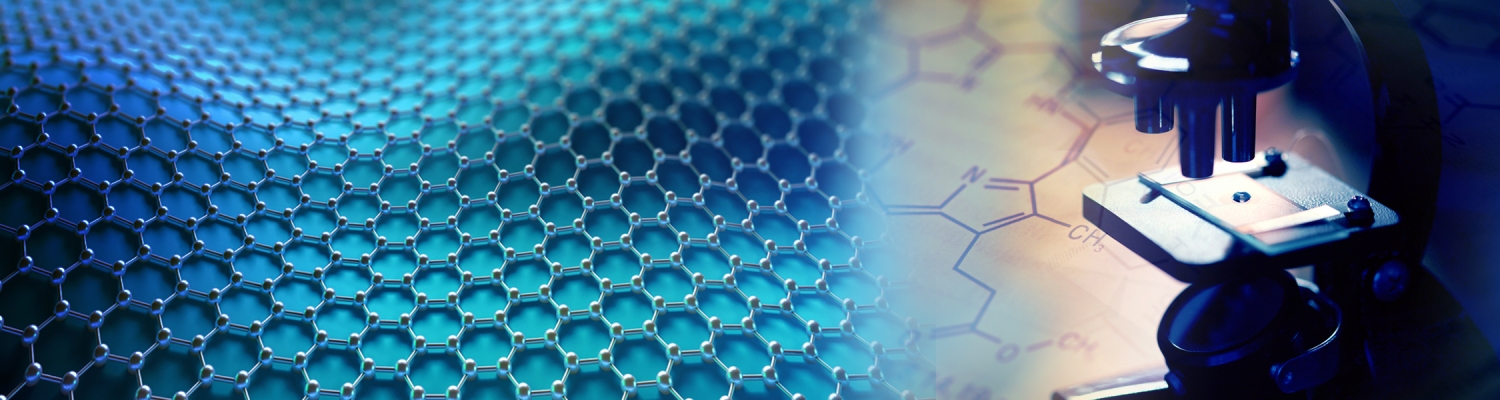
ISSN: 2641-6921
Bouaziz O1,2*, P Barges3
Received: June 26, 2020; Published: July 24, 2020
*Corresponding author: Bouaziz O, Laboratoire d’Etude des Microstructures et de Mécanique des Matériaux (LEM3), CNRS, Université de Lorraine, Arts et Métier Paris Tech, F 57000, Metz, France
DOI: 10.32474/MAMS.2020.03.000156
For High Strength Low Alloy (HSLA) steels or for age-hard enable steels (miraging) the strengthening by precipitation is done before forming operation to increase the yield stress as much as possible. In this publication the advantages of a hardening thermal treatment after forming operation are investigated in a low-cost age-hard enable steel Fe-Si-Ti consistent with automotive application.
Keywords: Age-hard enable, Precipitation, Forming, Ductility
The high strength low alloy (HSLA) steels are a group of low
carbon steels with small amounts of alloying elements (as Ti, V,
Nb, etc.) to obtain a good combination of strength, toughness, and
weldability [1-3]. By the addition of micro-alloying elements (less
than 0.5 wt.%), HSLA steels are strengthened by grain refinement
strengthening, solid solution strengthening and precipitation
hardening [4-8]. Regarding automotive applications, the entire
range of HSLA steels are suitable for structural components of
cars, trucks, and trailers such as suspension systems, chassis, and
reinforcement parts. HSLA steels offer good fatigue and impact
strengths. Given these characteristics, this class of steels offers
weight reduction for reinforcement and structural components
[9-11]. Despite the interest of HSLA, the precipitation hardening
is about 100MPa. So the new targets concerning the CO2 emission
of vehicles push the steel-makers to develop Advanced High
Strength Steels (Dual-Phase, Transformation Induced Plasticity)
hardened by multiphase microstructures containing 10 to 100% of
martensite [12] which offer a better combination between strength
and ductility for an acceptable cost Let’s notice that the Ultimate
Tensile Strength (UTS) increases more that the Yield Stress (YS).
YS is crucial for anti-intrusive aspect during a crash [12]. In the
other side, because there is no phase transformation in Aluminum,
age-hardening by precipitation is widely used in Aluminium alloys
hardened by various additive elements [see [13] for a review]. The
volume fraction of precipitates is several percent’s, the hardening
can be increased up to 400MPa, but the ductility decreases rapidly.
In steel, there is only miraging steels which are strengthened
by a massive precipitation of a martensitic matrix [see [14] for a
review]. Despite the impressive YS (up to 2.5GPa), the uniform
elongation is less than 1%. Consequently, no forming operation is
possible. In addition, the high contents of nickel (about 18%), of
molybdenum and of cobalt make these steels very expensive and so
they are never used in automotive industry. On the contrary, in the
60’s authors investigated other kind of steels suitable to be strongly
hardened by massive intermetallic precipitation without extracost
[15,16]. Among the different investigated system, the Fe-Si-Ti
alloys are the most promising. This is the reason why a series of
publications has been dedicated to this system in the 70’s by Jack&al.
[17-19]. Unfortunately, hardness and compression behaviour have
been only reported and a lot of discussions concerned the nature of the precipitates (Fe2Ti, FeSi, or Fe2SiTi) have been reported. More
recently a systematic study of precipitation kinetics in a Fe-2.5%Si-
1%Ti alloy in the temperature range 723 K to 853 K (450°C to 580°C),
combining complementary tools transmission electron microscopy
(TEM), atom probe tomography (APT), and Small-Angle-Neutron
Scattering (SANS)) have been carried out [20]. It has been shown
that the Heusler phase Fe2SiTi dominates the precipitation process
in the investigated time and temperature range, regardless of the
details of the initial temperature history.
Figure 1: Summary of the different strategies for the use of precipitation hardened steels: The green arrow is the usual one, the orange is the strategy developed in this publication.
Considering that the ductility decreases regularly as a function of the hardening up to 1.2GPa and because it is targeted to obtain a steel suitable for deep drawing the strategy showed in (Figure 1). (orange arrow) has been investigated. The objective is to form a material as soft as possible and as ductile as possible and to obtain the hardening by a thermal treatment after forming. This publication presents the characterization of this way to manage the situation. It is noticed that as Si and Ti promote ferrite, there is no phase transformation whatever the thermal treatment. (Figure 1) Summary of the different strategies for the use of precipitation hardened steels: The green arrow is the usual one, the orange is the strategy developed in this publication.
In order to assess for the first time in steel for automotive applications, the hardening have been chosen followed a thermal treatment at 500°C for two hours consistent with the kinetic determined by SANS [20]. As shown in (Figure 2). illustrating the tensile behavior of the steel consisting only in solid solution (i.e. only after recrystallization) is very ductile as for IF steels but with a higher yield stress due to solid solution hardening. After treatment and hardening of 300MPa is obtained with promising ductility. As shown in (Figure 3) the treatment has induced the expected massive precipitation of Fe2SiTi (3.8% weight percent with a radius of 4nm determined by TEM and SANS [20]). To assess the metallurgical route, the (Figure 4). shows that it is possible to severely bend the steel consisting only in solid solution without any defect up to an angle of 180°. Hardness trough the thickness has been measured before and after the thermal treatment (Figure 5). The value confirms the hardening by precipitation. It is noticed that tis precipitation hardening is not sensitive to the strain hardening induced by bending trough the thickness. Because the alloy is dedicated to automotive industry, the drawing must be investigated. This the reason why a cup obtained by deep drawing of 5cm diameter has been manufactured using the steel consisting in solid solution without any problem as illustrated in (Figure 6). It confirms the very high ductility before heat treatment. One another problem in automotive industry is the increase in spring-back with an increase in strength. In addition, it is very difficult to predict or to model this phenomenon. As shown in (Figure 7). this aspect has been studied by a standard test base the forming of a hat-shaped part. It is highlighted that the spring-back during the treatment is weak. That is probably because there is no phase transformation during precipitation and so no internal stresses.
Figure 3: TEM micrography showing the massive precipitation of Fe2SiTi after 2 hours at 500°C (the composition have been determined by APT [20]).
Figure 5: Hardness measurement trough the thickness of the fully bent specimen (i.e. angle of 180°) before and after heat treatment.
For the first time in steel industry for automotive industry a low cost age-hard enable steel has been studied following a strategy based on forming operations before the heat treatment. The bending, the drawability and the spring-back have been investigated highlighting promising results. In addition, the alloy exhibits a cost acceptable for automotive industry. In the future crashworthiness and weldability should be assessed after heat treatment. One of the last advantages is that a lot of parts can be treated at the same time in a furnace usually dedicated to tempering treatment.
Bio chemistry
University of Texas Medical Branch, USADepartment of Criminal Justice
Liberty University, USADepartment of Psychiatry
University of Kentucky, USADepartment of Medicine
Gally International Biomedical Research & Consulting LLC, USADepartment of Urbanisation and Agricultural
Montreal university, USAOral & Maxillofacial Pathology
New York University, USAGastroenterology and Hepatology
University of Alabama, UKDepartment of Medicine
Universities of Bradford, UKOncology
Circulogene Theranostics, EnglandRadiation Chemistry
National University of Mexico, USAAnalytical Chemistry
Wentworth Institute of Technology, USAMinimally Invasive Surgery
Mercer University school of Medicine, USAPediatric Dentistry
University of Athens , GreeceThe annual scholar awards from Lupine Publishers honor a selected number Read More...