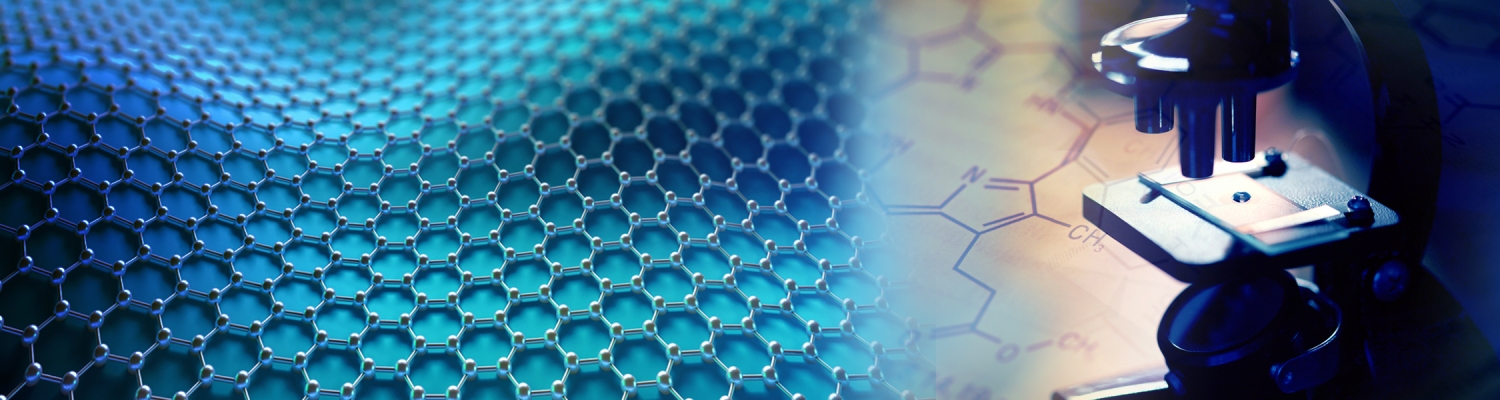
ISSN: 2641-6921
Hideo Nakajima1,2*
Received: April 21, 2021; Published: May 04, 2021
*Corresponding author: Hideo Nakajima, Institute for Lotus Materials Research Co., Ltd., Kitaku, Osaka 530-0001, Japan
DOI: 10.32474/MAMS.2021.04.000181
Recent development of fabrication methods of porous metals with open channels are introduced. Open-channel aluminum was fabricated by extracting template wires coated with lubricant out of solidified aluminum. The lubricant serves as a diffusion barrier between template wire and its surrounding aluminum. The penetration ratio of the through-holes is 100%. The hole size, hole length and porosity are uniquely controlled by thickness, length, and the number of template metallic wires, respectively. The methodology for producing the open-channel metals is expected opportunities for application technologies such as functional materials like heat sinks, heat exchangers, shock absorbing materials and light-weight structural materials.
Porous and foamed metals exhibit various characteristics such as flow channels, low density, large surface area and shock absorber which differ from dense metals. These characters can be utilized to heat dissipation devices, light-weight materials, catalyst carriers, electrodes, acoustic energy damping materials, impact energy absorption materials, etc. [1-4] Most of the porous metals possess isotropic, polyhedral pores, while lotus-type porous metals and open-channel metals have long elongated pores. The elongated pores can be utilized as fluid flow channels through which coolants transport. Long flow channels are indispensable for manufacturing products such as heat sinks and heat exchangers. The openchannel metals have been fabricated by powder sintering [5,6], solidification [7-9], mechanical drilling [10] and laser ablation [11] techniques. However, none of them satisfy the requirements for low-cost and time-efficient production of open-channel metals. The present author, Nakajima, succeeded in fabricating open-channel aluminum with long elongated channels [12,13]. In this review, the fabrication method of open-channel aluminum through extraction of lubricated metallic wires is described.
Figure 1: Schematic drawing of the fabrication of open-channel aluminum by the extraction of lubricated metallic wires. (a) lubricated wires are mounted in a crucible together with solid aluminum, (b) in the electric furnace the molten aluminum is filled up into the space among the wires in air, (c) after solidification, the aluminum ingot is taken out, and (d) the embedded wires are extracted to produce the open-channel aluminum [12].
Wires of stainless steel, copper, platinum, and molybdenum were used as templates of open-channel formation. The thickness of the wires was in the range from 0.28mm and 3.2mm in diameter. Boron nitride was sprayed onto the wires as a releasing agent with a thickness as much as 20 μm. A set of lubricated wires was mounted onto a graphite disc, which was inserted into a graphite crucible as shown in (Figure 1a). Aluminum was melted for 360s at 953K in atmospheric air, which was then dropped down to fill the space among the wires as shown in (Figure 1b & 1c). The solidified aluminum ingot was taken out from the crucible. The embedded aligned wires were extracted as illustrated in (Figure 1d) and open-channel aluminum was fabricated, whose three-dimensional images were measured by X-ray Computed Tomography as shown in (Figure 2a & 2b))[12].
Figure 2: (a) Open-channel aluminum: hole diameter 1.0mm in diameter and the porosity 30%, and (b) X-ray CT scanning image : hole diameter 1.0mm in diameter and the porosity 26%.
The hole diameter and porosity of open-channel aluminum shown in (Figure 2a) are 1.0mm and 30%, respectively. The porosity p is estimated from the open-channel aluminum whose height is l:
where dh is the diameter of the holes, x and y are the length and width of rectangle cross section of the open-channel aluminum, respectively, and n is the number of holes in the volume [12]. When the template wires are embedded into liquid aluminum, interdiffusion usually takes place between template metal and aluminum so that the template wires adhere to the solidified aluminum and cannot be extracted from the aluminum. Nevertheless, the template wires can be extracted, because the lubricant of boron nitride is operated as a diffusion barrier to suppress the alloying. If interdiffusion occurs between the solid wires and molten aluminum immersed into the space among the aligned wires, the zone width of alloying due to interdiffusion is evaluated from the available diffusion data. The interdiffusivity can be expressed in terms of
where c and D are the composition and the intrinsic diffusivity, respectively. The subscripts of Al and M indicate aluminum and metal, respectively. The diffusivity in liquid metals above their melting temperature is around 10-9 m2/s, which is several orders of magnitude higher than that in solid metals just below their melting temperature. Therefore, 10-10 m2/s 10-9 m2/s. The diffusion distance for 360s during aluminum melting is estimated as 0.4 mm 1.2 mm, where t is the time interval. Unless the boron nitride lubricant exists at the interface, the metallic wires adhere to the aluminum and extraction of the wires is impossible due to the formation of alloying phases. However, this is not the case in the present experiments. Thus, it is concluded that the boron nitride was served as a diffusion barrier and prevented interdiffusion [12]. (Figure 3a) shows X-ray CT scanning images of open-channel aluminum with spiral hole, while (Figure 3b) shows a picture of the template stainless steel wire with spiral shape before the wire was embedded into aluminum. The hole configuration is unique to the open-channel fabrication technique. The conventional perforation techniques such as sintering by space-holder method [5,6], directional solidification [9], core-bar pulling method [7], rod-dipping process [8], mechanical drilling [10] and laser ablation [11] processing perforate only straight pores or channel holes, because those use straight tools, straight beams, and unidirectional solidification. On the other hand, the present technique can produce not only straight holes but also curved holes and is thus capable of providing unique open channels.
Figure 3: (a) X-ray CT scanning image of spiral shaped hole of open-channel aluminum, and (b) template wire of 0.85mm in diameter before embedded in aluminum.
Open-channel metals are fabricated by extraction of template wires embedded in metals, which is simple, time-efficient perforation technique. Open-channel metals possess long elongated straight or spiral channel holes. These metals are expected to be used for various industrial applications.
Bio chemistry
University of Texas Medical Branch, USADepartment of Criminal Justice
Liberty University, USADepartment of Psychiatry
University of Kentucky, USADepartment of Medicine
Gally International Biomedical Research & Consulting LLC, USADepartment of Urbanisation and Agricultural
Montreal university, USAOral & Maxillofacial Pathology
New York University, USAGastroenterology and Hepatology
University of Alabama, UKDepartment of Medicine
Universities of Bradford, UKOncology
Circulogene Theranostics, EnglandRadiation Chemistry
National University of Mexico, USAAnalytical Chemistry
Wentworth Institute of Technology, USAMinimally Invasive Surgery
Mercer University school of Medicine, USAPediatric Dentistry
University of Athens , GreeceThe annual scholar awards from Lupine Publishers honor a selected number Read More...