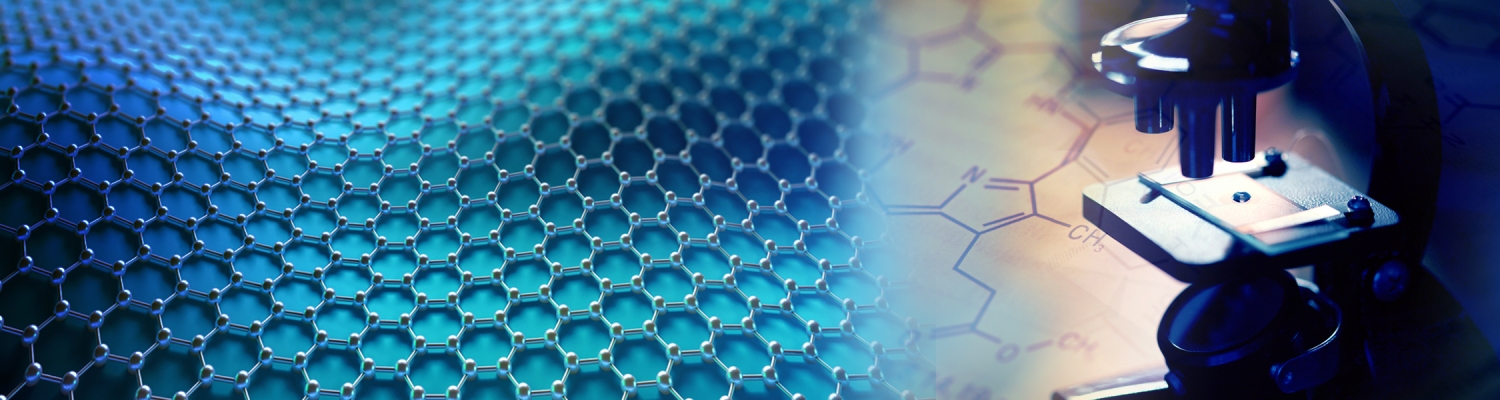
ISSN: 2641-6921
Bahman Zohuri*
Received:June 15, 2021; Published: August 3, 2021
*Corresponding author:Bahman Zohuri, Galaxy Advanced Engineering, Chief Executive Officer (CEO), San Mateo, California 94401, USA
DOI: 10.32474/MAMS.2021.04.000190
An electromagnetic pump is a pump that moves liquid in form of metal in particular, any electrically conductive liquid using electromagnetism phenomena. By law of physics of electromagnetic, a magnetic field can be defined as a set at right angles to the direction the liquid moves in, while a current is passing through it as well. This events, induce an electromagnetic force for the movements of the liquid. Applications of electromagnetic pump is including pumping liquid metal through any cooling system that are installed inside of liquid metal container in particular. Electromagnetic (EM) sodium and NaK pumps have a long history of extensive technology and successful use as an auxiliary system pumps and also as heat transport system pumps in some early research and small prototype Liquid Metal Fast Breeder Reactor (LMFBR) plants and for that matter in Liquid Metal Fast Reactor (LMFBR) such as Versatile Test Reactor (VTR) in recent years. These pumps started in latte applications is around 6500 gram per minute pump (gpm) rate.
Keywords: Electromagnetic Pump; Liquid; Heat Transfer; Neutronic; Electric Current; Pumping Liquid Metal
Electromagnetic Pumps are passive pump system and have been integrated in use for pumping liquid sodium in auxiliary cooling circuits such as fill and drain from the container of such metallic liquid, and purification circuits of sodium cooled fast breeder nuclear reactors, such as Liquid Metal Fast Breeder Reactor (LMFBR). However, it has been known that these pumps are not very efficient means of pumping any liquid, but despite their low efficiency these pumps are integrated and used in fast breeder nuclear reactors because of their high reliability and low maintenance due to absence of moving parts and that is why they are considered as a passive system. Besides, EM Pumps can be augmented for pumping impure sodium. For example, Indira Gandhi Centre for Atomic Research (IGCAR) institute has developed electromagnetic pumps of various capacities and successfully utilized them in experimental facilities. Sodium is used as a coolant in fast breeder reactors because of its excellent neutronic and heat transfer characteristics. Sodium is a fairly good conductor of electricity also and this has led to development of many electromagnetic sensors and devices for use in liquid sodium. One such device is the electromagnetic pump which is used to pump liquid sodium in auxiliary circuits of a fast reactor and in various test facilities
Though centrifugal pumps are used for pumping sodium in the primary and the secondary circuits of the reactor, electromagnetic pumps have been preferred in the auxiliary circuits. Low efficiency of these electromagnetic pumps prohibits their use in the main sodium circuits of a fast reactor. But their ability to operate even with impurities in sodium and their high reliability and almost maintenance free operation makes them an ideal choice. These electromagnetic pumps work on the principle that whenever a current carrying conductor is placed in a perpendicular magnetic field a force act upon it. There are various types of electromagnetic pumps which can be mainly classified as conduction electromagnetic pumps and induction electromagnetic pumps [1]. In conduction electromagnetic pumps 1-2 the electric current in sodium flows via conduction from an external circuit which requires physical connection of the external circuit to the duct whereas in induction pumps, the current is induced in sodium without connecting an external circuit to the Stainless Steel (SS) duct. Since no physical contact is there with SS duct in case of induction pumps, they are considered to be more reliable compared to conduction pumps. Both the conduction and induction types of pumps have been developed and are in operation in Indira Gandhi Centre for Atomic
Research (IGCAR). Induction pumps are mainly of two typesthe Flat Linear Induction Pump (FLIP) and the Annular Linear Induction Pump (ALIP) [2]. FLIP has a flat duct with stator normally on upper and lower part of the duct. It also has rectangular copper bars welded on its sides for providing a low resistance short circuit path and thereby increasing its efficiency. Besides, the flat duct is less suitable for high pressure applications therefore it was decided to use ALIP for Secondary Sodium Fill and Drain Circuit (SSFDC) of Prototype Fast Breeder Reactor (PFBR) presently under construction at Kalpakkam [3]. This pump is of flowrate 170m3/h and can deliver a head of 4 kg/cm2. This paper describes the design data of the pump and details of the testing of pump carried out at the Steam Generator Test Facility (SGTF) in IGCAR.
Liquid metal loops are used for heat removal and for the study of certain magneto-fluidic phenomenon like MHD (Magneto-Hydro Dynamic) effects. These loops operate at high temperatures and carry fluids that are invariably toxic in nature. Ensuring the purity of fluid in a closed loop application needs non-intrusive pumps electromagnetic pumps. We have designed and analyzed a prototype electromagnetic pump to be used in mercury loop for carrying out various studies. This Electromagnetic pump is designed using permanent magnets which are mounted on periphery of rotor, which is rotated using DC motor. The liquid metal flows in a semicircular duct surrounding the rotor. See (Figure 1), where surface plot of magnetic field density superimposed with contours of magnetic potential of an electromagnetic pump simulated using Multiphysics software COMSOL®. A magnetic field ( rc b ) always exists around the current (I ) carrying conductor. When this current carrying conductor is subjected to an external magnetic field ( rap B ), the conductor experiences a force perpendicular to the direction of I and rap B . This is because the magnetic field produced by the conductor and the applied magnetic field attempt to align with each other. A similar effect can be seen between two ordinary magnets. This principle is used in an electromagnetic pump. The current is fed through a conducting liquid. Two permanent magnets are arranged to produce a magnetic field rap B as shown in the (Figure 2). The supplied current has a current density (J ) and the magnetic field associated with this current can be called as ‘Reaction magnetic Field ( rc b )’. The two magnetic fields rap B and rc b attempt to align with each other, thus this causes mechanical motion of the fluid as illustrated in (Figure 2). As we stated at the introduction of this appendix, a special type of liquid metal thermo-magnetic device is the Annular Linear Induction Pump (ALIP). It is known that electromagnetic pumps have a number of advantages over mechanical pumps: absence of moving parts, low noise and vibration level, simplicity of flow rate regulation, easy maintenance, and so on. However, while developing induction pumps, in particular ALIPs, we are faced with a significant problem of Magneto-Hydrodynamics (MHD) instability arising in the device. The manifestation of the instability does not allow linear induction pump development in a certain range of flow rate or the development of high efficiencies under certain flow rates and dropping pressure conditions.
Linear induction pumps use a traveling magnetic field wave created by 3-phase currents, and the induced currents and their associated magnetic fields that generate a Lorentz force (see (Figure 3). The 3-phase winding arrangement for the solenoids usually follows the sequence AA ZZ BB XX CC YY where A, B, C denote the balanced 3-phase winding and X, Y, Z the opposite phase; for a direct balanced system, if A = 00 , B=1200 , and 0 C = 240 then X =1800 , Y = 3000 and Z = 600 . The correct winding sequence for the solenoids is obtained by arranging the sequence by the rising phase: AA ZZ BB XX CC YY. The complex flow behavior in this type of device includes a time-varying Lorentz force and pressure pulsation due to the time-varying electromagnetic fields and the induced convective currents that originate from the liquid metal flow, leading to instability problems along the device geometry. The determination of the geometry and of the electrical configuration of a thermomagnetic device gives rise to an inverse magnetohydrodynamic field problem. When the requirements of the design are defined, this problem can be solved by an optimization technique. In (Figure B-3), ALIP, annular linear induction pump; (Figure B-3(B)) shows the cross section of the ALIP, and it is an adaptation of a diagram originally drawn by Dong Won Lee, KAERI, Korea Atomic Energy Research Institute. This is adapted with permission [4]. The objective function which must be maximized in the optimization problem is derived from the main design requirement. Usually for an MHD device, this is the efficiency. Other design requirements can be taken, into account as constraints. For a nonlinear system, such as for linear induction pumps, the main objective functions are low weight and high efficiency and so more than one maximum can exist. In this case a technique for global optimization must be used.
In a typical electromagnetic pump, the following basic principles do works as follows and can illustrated by (Figure 4) as:
a. Liquid metal are conductors.
b. Based on the Fleming’s Left-Hand-Rule.
c. Current flowing vertically through the liquid metal experiences a force ( F = I L×B ).
As it is illustrated in (Figure 5), more details and types of EM pump are revealed including different components involved with infrastructure of these types of pumps, that is used as part of cooling system in liquid metal breeder fissionable nuclear reactors [5].
Types of Electromagnetic pumps includes:
a. Conduction Pump: In this case current is directly conducted into fluid through electrodes. Two variants, Alternative Current (AC) and Direct Current (DC).
b. Induction Pump: Current in the conducting fluid is induced by
a traveling magnetic field.
c. Thermoelectric Pump: Current flowing through the liquid metal is derived directly from the thermal power contained in the hot liquid metal flow, such as the one that we can encounter in Liquid Metal Fast Breeder Reactor (LMFBR) of Generation III like French built Phoenix-II or Liquid Metal Breeder of Generation IV, such as Molten Salt Reactor (MSR) Sodium Cooled Fast Reactor (SFR). See Chapter 2 of the book by Zohuri [5].
As far as holistic observation of EM pump application is concerned, Figure-6 presents such general application of device as two main driven scenario and they are:
a. Cooling of nuclear reactor.
b. Pouring and transportation of high temperature metals in foundry
If we take look at Electromagnetic pump form inside point of view as it is depicted via (Figure 7), we notice that the electrical current is induced by transformer action. The transformer’s primary coil presented in (Figure 7) is connected to an AC singlephase power source. The transformer pole pieces are arranged in the shape of a picture frame and server as the carrier of magnetic flux. The transformer secondary winding around the bottom leg of the picture frame as it is shown in (Figure 7) is molten metal and is formed by channels in ceramic parts. The turns ratio amplifies the electrical input current to produce very high amperage in the molten metal. (Figure 8) is demonstration of a sectional view of electromagnet construction that is added, which consists of a C -Shaped pole piece and two excitation coils. The opening in the C straddles the necked-down section of the molten secondary turn, so the magnetic field H crossing the pole gap is perpendicular to the secondary current I , resulting in force Q to move metal through the pump. In (Figure 9), we see the complete electromagnetic pump from inside perspective of infrastructure. It is surrounded by or encapsulated in ceramic parts to protect it from molten metal contact to prevent any corrosions or any other side effects from liquid metal of internal nuclear core. Pump output Q is varied by controlling input power and can be regulated from almost dropwise flow up to full bore delivery.
Like all other electromagnetic pumps Annular Linear Induction Pump (ALIP) works on the principle that whenever a current carrying conductor is placed in a perpendicular magnetic field a force acts on the conductor. The magnitude of this force is given by F=BIL, where “I” is the current through the conductor, L is the length of the conductor and B is the magnetic flux density in which the conductor is placed. In the case of ALIP, there is an annular region in which sodium flows, outside this annular region there are copper windings which are excited by 3-phase AC supply and produces a linearly moving magnetic field. This linearly moving magnetic field, according to Faraday’s Law of induction, induces a current in the liquid metal (Figure 10). The interaction of this current and moving magnetic field produces a force on the sodium resulting in the pumping action as illustrated in (Figure 10), where it shows the working principle of Annular Linear Induction Pump [6]. Since the working principle of ALIP is similar to an induction motor, the equivalent circuit of ALIP (Figure 11) is also similar. At the same time there are some differences as compared to an inductor motor. Typical slip in induction motors is 0.05 or less whereas for ALIP typical slip is in the range 0.4-0.9 which leads to higher slip losses. The presence of ducts for containing sodium not only introduces additional resistive elements in the equivalent circuit but also leads to higher air-gap compared to that in an induction motor. These features lead to reduction in power factor and in efficiency when compared to that of an induction motor. Besides, end effects and hydraulic losses also lead to reduction in efficiency [6].
In (Figure 11), the following parameters do apply as: a. Resistance of Stator Winding b. Leakage Reactance of Stator Winding c. Magnetic Reactance d. Fluid Resistance e. Resistance of Inner Duct f. Resistance of Outer Duct g. Air-Gap Electromagnetic Force (EMF) h. Slip i. 1 R -- Resistance of Stator Winding ii. 1 X -- Leakage Reactance of Stator Winding iii. m X -- Magnetic Reactance
iv. f R -- Fluid Resistance v. j R -- Resistance of Inner Duct vi. w R -- Resistance of Outer Duct vii. E -- Air-Gap Electromagnetic Force (EMF) viii. s -- Slip Note that: The winding in the ALIP is circular pan-cake type and is different from conventional winding used in rotating induction motors.
There exist some advantages to utilization of this pump in any application, where these EM pumps are installed, while along with such pros there exist some limitation for these pumps, and they all listed below. Advantages a. No moving parts, no vibrations or wear and tear b. No seals, no splits c. Less maintenance and more reliable d. Safe to be used Limitations a. Power losses due to back EMF, Ohmic heating. b. Limited uses since very few liquids are good conductors of electricity.
In conclusion, we can claim that EM pumps, are one of the best passive choice without integration of any external source of energy for moving parts to movie liquids from one side to another, specially, when are dealing with liquid metal environment, where we need heat transfer to take place. They rely on physics of electromagnetism phenomena for this purpose.
Historically, 53-psi linear induction Electromagnetic Pump (EMP) has been in operation for years in the Experimental Breeder Reactor-II (EBR-II) intermediate sodium heat transfer system. EBRII is a sodium -cooled fast reactor designed, built and operated by Argonne National Laboratory at the National Reactor Test Station in Idaho as illustrated in (Figure-12) [7]. This reactor was shut down in 1994 and custody of the reactor was transferred to Idaho National Laboratory (INL) after its founding in 2005.“Mechanical centrifugal-type pumps have been the general choice for higher flow capacity service in larger prototype liquid metal fast breeder reactor (LMFBR) power plant heat transport systems. The fact that their efficiency is approximately 50% greater than that of the EM pump has been viewed as an important consideration for larger plants designed to demonstrate commercial performance potential. However, it is evident that problems encountered in exposure of mechanical pumps to the high temperatures and thermal transients of primary sodium heat transport systems become more severe as plant and pump sizes increase” [8]. “The EPRI-sponsored 1000- MW (e) pool-concept LMFBR plant design studies reported in EPRI reports NP-1014, NP-1015, and NP-1016 reveal additional areas of concern related to mechanical primary pump installation support and sealing requirements unique to the pool configuration. Furthermore, the pump drive motors are large contributors to congestion of above-deck equipment that may aggravate major equipment maintenance problems in the head access area of a pooltype plant” [8].
J. F. Cage report [8], also was indicating and to obtain a preliminary assessment of the potential applicability and desirability of the ac (linear induction) EM pump as an alternate option that may substantially alleviate these pool-concept plant problems. Furthermore, the EM pump is mechanically passive and has unique operating and control characteristics; therefore, additional potential benefits in the areas of system operability, pump reliability, and pump maintenance requirements were foreseen. It was anticipated that the impact of the lower efficiency of these EM pumps on plant economic performance will be moderate and judged acceptable in view of potential benefits. For this proposed conceptual application in the approach idea of metal liquid pooconcept nuclear power plant, electromagnetic pump is submerged in the primary system and could also be used as a passive cooling safety device for backflow in a sodium liquid type metal reactor that it pumps. For this uncommon arrangement, cooling of the pump and accommodation of the temperature conditions are critical problem areas that needs to be resolved as well [8].
However, designer of just fast liquid metal reactors as part of their project, should take into consideration, by assessing of benefits versus the costs of using EM pumps instead of mechanical pumps should eventually be determined in terms of effect on the net cost of the electrical energy delivered to the network by the plant, including the capital cost factor. Because plant layout and comparative capital cost studies were beyond the scope of this brief study, the economic impact of using EM pumps is stated only in terms of effect on net plant efficiency. The use of electromagnetic pumps in both primary and intermediate heat transport systems in the reference plant was found to reduce the overall plant efficiency by 0.4%, or 137 btu/kwhr. The development of high-voltage hightemperature insulation systems and further design optimization work were identified as necessary if the advantages of the EM pumps are to be fully utilized in large LMFBR’s and was considered as part of clinch river project by advanced reactor division of Westinghouse corporation in 1987 and was investigated by this author (i.e., Zohuri) at Waltz Mill Pennsylvania. As part of this investigation and results obtained by the JF Cage report performed an evaluation application of Linear Induction Electromagnetic (LIEM) sodium pumps to the heat transport systems of 1000 Mwe pool-type sodium-cooled fast breeder reactor power plant.
In this evaluation, characteristics of EM pumps were examined to evaluate their size and effect on plant efficiency, the arrangement of the primary heat transport system, and their potential advantage in mitigation of SCRAM temperature transients of LMFBR type reactors. Both gas-cooled pumps and pumps using high temperature insulation and cooled by the pumped sodium were studied. The parameters that establish size limitations were identified and several scoping arrangements designs were made. It was concluded that electromagnetic pumps are smaller and lighter than equivalent mechanical pumps, and that these features can be utilized to minimize the size and complexity of the primary heat transport system.
The Versatile Test Reactor (VTR) is a project currently in development by the U.S. Department of Energy to build a fastneutron test reactor by 2026 as conceptually, depicted in form of 3-D, in (Figure 13). Historically, after the Fast Flux Test Facility (FFTF) and the Experimental Breeder Reactor-II (EBR-II) were decommissioned in 1992 and 1994, respectively, the United States was left with no fast-neutron reactor in its fleet. Fast-neutron research was limited to a few restricted reactors located in Russia, including the Bor-60 [9]. To address this problem Nuclear Energy Innovation Capabilities, Act of 2017 included a provision directing the Department of Energy to begin planning for a fast-neutron source. In February 2019, the U.S. Department of Energy announced its plans to build a Versatile Test Reactor, or VTR as illustrated in (Figure 14). This new research reactor will be capable of performing irradiation testing at much higher neutron energy fluxes than what is currently available today. This capability will help accelerate the testing of advanced nuclear fuels, materials, instrumentation, and sensors. It will also allow DOE to modernize its essential nuclear energy research and development infrastructure and conduct crucial advanced technology and materials testing necessary to reenergize the U.S. nuclear energy industry.
The VTR is a state-of-the-art research and development facility that creates the conditions necessary to test how well fuels, materials and sensors endure when battered with radiation in the form of fast neutrons.
The likely design will be a sodium-cooled 300 megawatt reactor based on GE-Hitachi’s PRISM reactor. The proposed first fuel will utilize a uranium-plutonium-zirconium alloy fuel. Such an alloy fuel was tested previously in the EBR-II reactor. Later reactor fuel could consist of other mixtures and varying enrichments of uranium and plutonium and could use other alloying metals in place of zirconium.[10] There are no power generating facilities planned for the VTR [11]. By the nature of the design for VTR, in principle such a “fast reactor” could also convert non-fissile Uranium-238 to Plutonium-239, which could be extracted by reprocessing the fuel. Many nuclear engineers envision a future in which the world relies on such fast reactors and reprocessed fuel for its electricity. Critics of the nuclear industry argue that breeder reactors are unnecessary and risky, as they would establish an economy in plutonium, the stuff of nuclear weapons. Some critics say the VTR is a way to keep that controversial dream alive—although VTR developers do not plan to breed plutonium or reprocess fuel. In nutshell, VTR is considered a Liquid Metal reactor and is an excellent candidate for integration of a proper EM Pump (EM) for both primary and backflow cooling device as a passive system that does not require any mechanical moving part in it.
Note that with interest in augmentation of Nuclear Micro Reactor (NMR) in space that is on rise by U.S. Department of Defense, scientist, and designer of this type of reactor are looking at integration of EMP in such reactors as primary cooling system in addition to a passive cooling system, such as Heat Pipe (HP). [12- 15]
Depending on the application of liquid metal reactor, different configuration of EM pump could be taken under considerations and may include in the evaluations of pump such as Flat Linear Induction Pump (FLIP) in two different arrangements of the Annular Linear Induction Pump (ALIP): One with a single fluid passage (Once Through, or O.T.), and one with a central return passage (Center Return, or CR). Detailed of such design and size consideration are beyond the scope of this paper Note that: Within the range of flow and head parameters of interest here, linear induction. EM pumps are generally smaller than mechanical pumps of the same rating.
Mechanical pumps tend to complicate the design of the reactor deck structure if our intention is toward Smaller and Modalized Reactors (SMRs) in Advanced form with high temperature operating mode. The mechanical pumps impose heavy loads (e.g., 200,000 lb. per pump) on the deck while requiring both rigidity and an accurate alignment. The mechanical pump in a pool is inherently long (up to 50 feet) because as a minimum it must penetrate the eleven foot shield deck and extend through the cover gas into the cold pool sodium. The bearings are sensitive to small shaft misalignment angles, yet the deck and the submerged reactor support structure, both of which the pumps penetrate, experience several inches of horizontal and vertical displacement due to temperatures differentials which must somehow be accommodated. Translating or rotating joints at the deck mount and flexible bellows and sealed joints at the core support plates have been resorted to in pooltype reactor designs. While solving one problem, such features have introduced others such as undesirable seismic behavior. On the other hand, EM pumps avoid many of these problems. EM pumps are much shorter and about one third lighter in weight than mechanical pumps, because they combine the drive motor and hydraulic functions in one compact assembly. Thus, they can be mounted directly on the core support structure submerged in the cold pool and supplied with power through the deck. The length of the electrical cable conduit, a stainless steel pipe, allows it to be flexible enough to accommodate all thermal dilations between the deck and the core support structure.
Based on past design study of EM Pump (EMP) and its consideration design and sizing for a Liquid Metal Fast Breeder Reactor by General Electric (GE) advanced reactor past couple decades ago [8] as illustrated in (Figure 15), it can be concluded that:
1) An EM pump with high temperature insulation will reduce plant efficiency by 0.4% while the gas cooled pump arrangement will reduce it another 0.1%, compared to mechanical pumps.
2) A + 3% uncertainty in EM pump efficiency will result + 0.1% uncertainty in net plant efficiency.
3) A gas cooled EM pump design would substantially increase the required cooling capacity of the reactor building air conditioning system. The necessary large gas ducting in the reactor head area would also complicate the layout of piping arrangement and interfere with component maintenance activities.
Bio chemistry
University of Texas Medical Branch, USADepartment of Criminal Justice
Liberty University, USADepartment of Psychiatry
University of Kentucky, USADepartment of Medicine
Gally International Biomedical Research & Consulting LLC, USADepartment of Urbanisation and Agricultural
Montreal university, USAOral & Maxillofacial Pathology
New York University, USAGastroenterology and Hepatology
University of Alabama, UKDepartment of Medicine
Universities of Bradford, UKOncology
Circulogene Theranostics, EnglandRadiation Chemistry
National University of Mexico, USAAnalytical Chemistry
Wentworth Institute of Technology, USAMinimally Invasive Surgery
Mercer University school of Medicine, USAPediatric Dentistry
University of Athens , GreeceThe annual scholar awards from Lupine Publishers honor a selected number Read More...