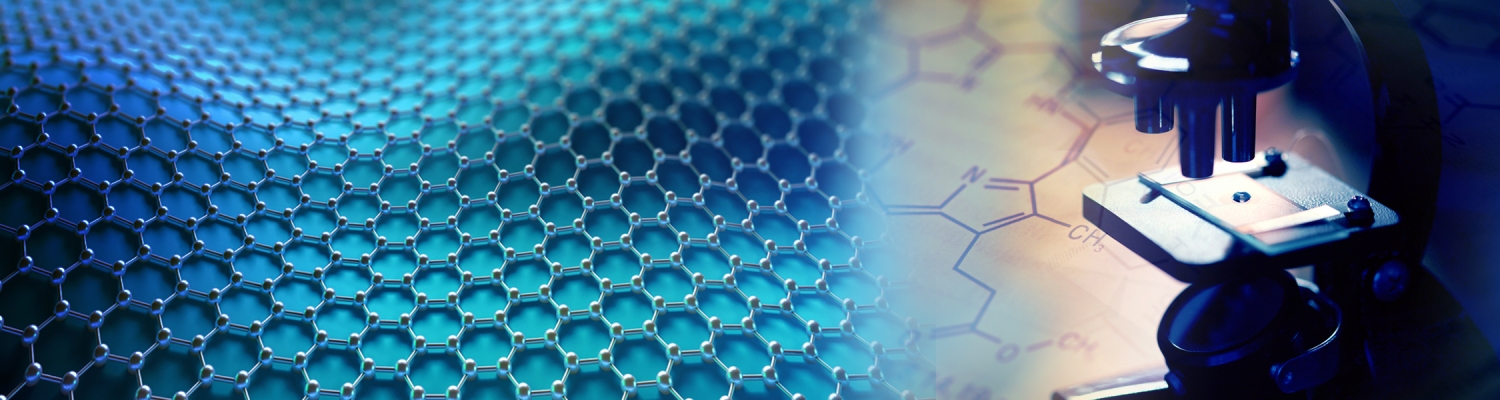
ISSN: 2641-6921
Bouaziz O*
Received: February 06, 2020; Published: February 19, 2020
*Corresponding author: Bouaziz O, Laboratoire d’Etude des Microstructures et de Mécanique des Matériaux (LEM3), CNRS, Université de Lorraine, Arts et Métier Paris Tech, France
DOI: 10.32474/MAMS.2020.02.000141
Thanks to the measurements of the Bauschinger effect and the twin volume fraction, the local stress within twins in Twinning Induced Plasticity (TWIP) steels has been experimentally determined. It is found that this local stress rapidly increases as a function of plastic strain to levels higher than 2GPa and can be probably higher than 3GPa for strains larger than 0.2. Mechanisms suitable to explain this order of magnitude are briefly discussed.
Keywords: TWIP, twin; Stress; Strain-hardening
Discovered by Sir Robert Hadfield in 1881 [1], high manganese TWIP steels are currently one of the most attractive materials for structural applications in the automotive industry due to their unique combination of strength and elongation. The impressive strain-hardening of TWIP steels is the most studied mechanical characteristic of these alloys [2]. It has been reported that these alloys exhibit a very large Bauschinger effect [3-5], which is the signature of a strong heterogeneous distribution of local stresses in the microstructure. Due to the nanoscopic size of these induced twins, it can be assumed that the local stress within these twins is larger than the stress within the surrounding matrix, bringing about a large strain-hardening with the continuous increase of the twin volume fraction [3-7]. Unfortunately, no experimental determination of the local stress of the twins has been possible up to now, by X-ray diffraction for instance, due to two main difficulties: the thickness of the twins is very small (20 to 200nm) and the twins and the matrix present the same chemical composition and crystallographic structure. The determination of these characteristics is of prime importance in order to improve the understanding of the relationship between the microstructure evolution and the mechanical properties of FeMnC TWIP steels. A methodology suitable to provide a range of local stress within the twins is thus reported in this study. The determined values are discussed in regards of known plasticity relaxation mechanisms.
This study focuses on a TWIP steel containing 1.2 wt.% of carbon and 20 wt.% of manganese. This austenitic alloy is completely stable at room temperature (i.e. no strain-induced ε-martensite is observed) with the activation of mechanical twinning during straining. The grain size of the cold rolled and annealed 1.4 mm thick sheets is around 20μm [7]. The mechanical behaviour along a non-monotonic strain-path has been investigated by reverse shear tests. The experimental procedure is described in detail elsewhere [8]. (Figure 1) shows the different Bauschinger tests that were performed. The reverse shear curves are represented with a positive flow stress and their corresponding accumulated forward-backward strain. The monotonic simple shear curve is also represented on this Figure. These curves are used to measure the Bauschinger effect BE and the back-stress sb given by:
(1)
Figure 1: Stress-strain curves of monotonic simple shear and reverse shear loading after different forward prestrain. Reverse curves are shown with a positive flow stress.
The evolution of the back-stress as a function of plastic prestrain is illustrated in (Figure 2) for offsets of 0.2%, 0.5% and 1%, respectively. It appears that the back-stress (i.e. the kinematic hardening) contributes up to half of the total strain-hardening which is consistent with previously reported results [3,4]. Such a large contribution can be described thanks to the microstructure evolution with strain of this TWIP steel, particularly the twin volume fraction and the characteristics of these twins. Indeed, the twin volume fraction has been measured following a procedure reported in [9]. In the case of simple shear loading, the volume fraction of twins has been determined at levels of equivalent strain of 0.1 and 0.2 [10]. Table 1 summarizes the characteristics estimated at these two levels of straining. Finally, it is worth noting that the twin thickness in the present TWIP steel has been estimated by transmission electron microscopy in the range 20 to 200nm [11,12]. Whatever the strain-hardening modelling [3,5,6], the general expression for the back stress (or kinematic hardening) resulting from the twins considered as a reinforcing phase is given by [13]:
(2)
Figure 2: Evolution of back-stress (as estimated by Eq.1) as a function of forward strain for different offsets.
Table 1: Experimental volume fraction of twin and back-stress deduced from Bauschinger effect as a function of equivalent plastic strain.
where F is the volume fraction of twins, σT is the average local stress within these twins and σM is the average stress within the untwined matrix. Furthermore, mechanical equilibrium imposes that
(3)
Where σ is the total flow stress. The average local stress within twins can therefore be expressed as a function of the measured stresses as:
(4)
And the average stress within the untwined matrix is:
(5)
The values of σT and σM are summarised in Tables 2 & 3 respectively. The evolutions of these stresses with the equivalent plastic prestrain are also drawn in (Figures 3&4). It is worth noting that the ratio between the local stress within twins σT and the total flow stress σ is constant and equal to about 3.6. It is worth noting that the determined local stress within the twins lies in the range of
(6)
Table 2: Local stress within twins in MPa as a function of the plastic prestrain and of the chosen offsets deduced from Bauschinger tests and measured twin volume fractions.
Table 3: Local stress within the matrix in MPa as a function of the plastic prestrain and of the chosen offsets deduced from Bauschinger test and measured twin volume fractions.
Figure 3: Evolution of the local stress within twins σT and flow stress σ as a function of equivalent strain deduced from Bauschinger test and measured twin volume fractions.
Figure 4: Evolution of the local stress within the matrix σM and flow stress σ as a function of equivalent strain.
where E is the Young modulus of 195GPa consistent with the paramagnetic state at room temperature related to the chemical composition of the investigated alloy. These bounds correspond to 1/3 to 1/2 of the theoretical strength for plasticity without any dislocation or for theoretical fracture stress. If plastic relaxation within twins was the emission of a dislocation, the maximum local stress would correspond to the critical stress for dislocation bowing to the critical Orowan configuration [14]
(7)
Using the values reported in Table 2, the twin thickness corresponding to st is close to 20nm, i.e. the lower bound of the measured thicknesses [11,12]. Conversely, a twin thickness of 200nm would bring about a critical stress around 200MPa, which is much smaller than the estimated twin stress (and also smaller than the yield strength). That means that the mechanical twins in TWIP steels present an internal structure strongly hindering dislocation glide as it was experimentally reported in [12] with a large density of sessile dislocations. Since the knowledge of the level of local stress within twins is crucial for significantly improving the understanding of the microstructure – properties relationships of FeMnC TWIP steels, a methodology suitable to determine this parameter has been developed. Experimental determination of the Bauschinger effect and the twin volume fraction combined with a suitable analysis provides for the first time the determination of the local stress within twins in Twinning Induced Plasticity (TWIP) steels. It is reported that this local stress increases as a function of plastic strain and is rapidly larger than 2GPa and can be probably larger than 3GPa for strains larger than 0.2. Twin stresses range between 30 to 50% of the ultimate theoretical strength and the critical stress for the emission of a dislocation, a level compatible with the reported twin internal structure. Finally, it was observed that the ratio between the local stress within twins σT and the total flow stress σ is constant and equal to about 3.6.
The author thanks Dr. F Levy for stimulating discussions.
Bio chemistry
University of Texas Medical Branch, USADepartment of Criminal Justice
Liberty University, USADepartment of Psychiatry
University of Kentucky, USADepartment of Medicine
Gally International Biomedical Research & Consulting LLC, USADepartment of Urbanisation and Agricultural
Montreal university, USAOral & Maxillofacial Pathology
New York University, USAGastroenterology and Hepatology
University of Alabama, UKDepartment of Medicine
Universities of Bradford, UKOncology
Circulogene Theranostics, EnglandRadiation Chemistry
National University of Mexico, USAAnalytical Chemistry
Wentworth Institute of Technology, USAMinimally Invasive Surgery
Mercer University school of Medicine, USAPediatric Dentistry
University of Athens , GreeceThe annual scholar awards from Lupine Publishers honor a selected number Read More...